Dock Slot Booking
1st December 2020
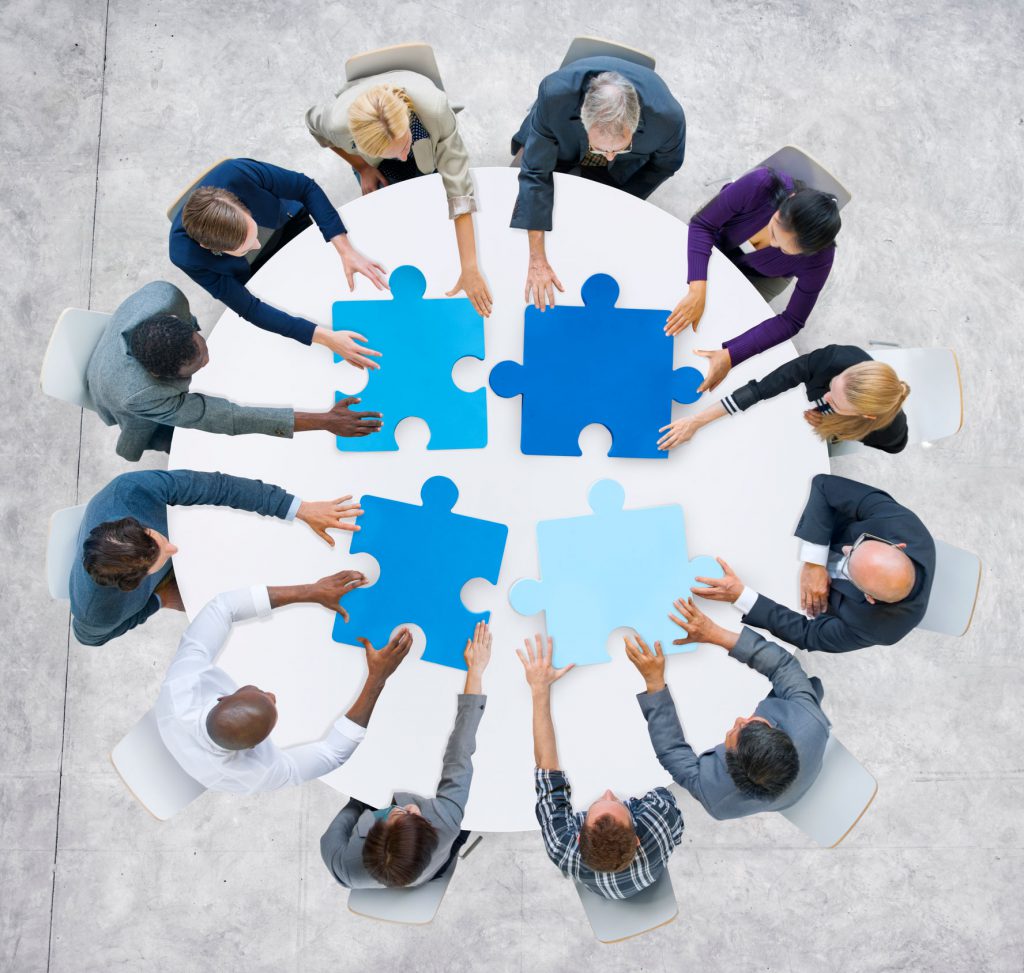
An easy-to-implement smart booking function can eradicate inconvenience and inefficiency at the warehouse unloading dock. Paul Hamblin reports.
Here’s the scenario. You’re running a warehouse with several trucks arriving every day. Trouble is, you don’t know exactly when a certain truck is coming and exactly what’s on it when it does. You can’t match it to the specific equipment that might be needed to unload it and you don’t know how many people from your side you need physically to perform that task, whether a small amount of pallets or whether a full truckload.
From an efficiency perspective, it would be very helpful if you knew that sort of information for the day in advance – approximately how many lorries are coming, how big they are, what they’re carrying and when to expect them. Are they carrying bulk goods or packed goods or something in between? You need to know these things so that you can be properly prepared with the equipment and people necessary to process the arrival quickly and cost-effectively. Vice-versa with an outbound pickup – you can have the goods ready to be loaded at the right dock at the right time.
Then think of the carrier – waiting patiently in line, the driver twiddling thumbs until their turn comes up. Not the best use of time for all parties. What you all need is something to plan and coordinate this effort, a single source of information available to all stakeholders, making life more efficient and cost-effective for shippers and transport and warehouse managers alike. With such a facility, speed and cost are both optimised, to the benefit of shipper, carrier and warehouse.
Step forward transport software specialist Alpega TMS with a slot management and dock scheduling software solution that is both quick and easy to implement. Carolyn Hunt, Alpega’s Brussels-based Director of Go to Market TMS, explains how it works: “It starts by creating a virtual twin of the inbound/outbound facility. It shows how many docks they have and what type of goods are loaded into those docks.The warehouse then sets up its schedule, to include working hours. Once that’s set, the carrier actually goes into the system with its proposed truckload. The system will
then automatically choose the right dock for that carrier to book, and the most appropriate available time slot for that location based on specific product requirements.”
Realtime warehouse visibility is enhanced by an easy-to-use, customisable interface. Jean-Yves Lemelle, Product Manager for Alpega TMS Smart Booking Solution, explains that user experience has been key to the success of the product (developed from the former Transwide solution) which was launched last year and which already has several blue-chip companies, including Maersk, onboard. Admin for shippers and carriers is reduced. “We try to provide an interface for warehouse users which gives them as many configurations as possible, so that they have inbound and outbound options available matching exactly what they wish. Then we focus on the experience of the carrier so that they have the least information possible to provide, yet giving them the most
optimal dock and time slot.”
A familiar USP of Alpega TMS is its modularity. It enables customers to move at the pace they wish on the digital journey. The tool can be bought as a stand-alone or as part of a complete suite of end-to-end TMS solutions. “A lot of shippers want to get started on that path of digitalization, and I think this is a good tool to get started with, because it can be implemented very quickly,” points out Carolyn Hunt. “It’s quite self explanatory and easy to use, and it shows immediate benefits, to both the shipper and the carrier.”
Jean-Yves Lemelle adds: “I think it’s also important to highlight that we’re committed to making this tool as self service as possible, enabled by having configurations that other competitive
products are not able to offer.”